Offsite Insights – Breaking down the Barriers
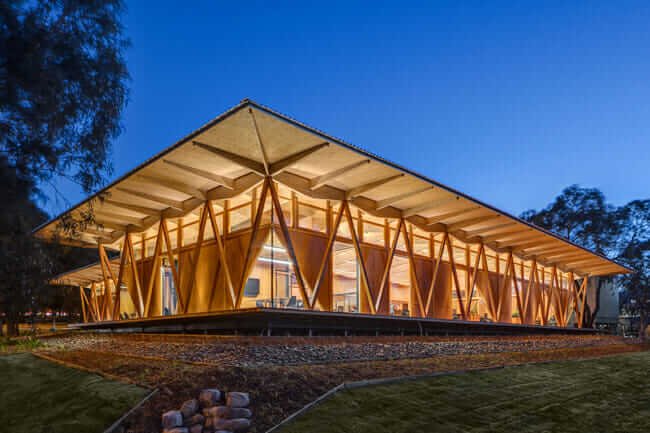
My previous piece in this series looked at the three P’s – Predictability, Precision and a Portfolio of works – the benefits an offsite approach can bring to a project. Today, we look to break down the barriers surrounding offsite, particularly the preconceptions that offsite approaches bring.
Unfortunately, there is a persistence of social stigma and preconceptions surrounding offsite approaches in Australia which we need to overcome. Such preconceptions lead to a nervousness, conservatism, reversion to business as usual and lack of willingness to adopt offsite approaches. Mark Farmer puts it down to “conservatism of many clients and often scepticism of advisors”.
I tend to point the blame towards the “demountable generation”, where invariably any mention of the word modular or volumetric automatically builds a preconception of cheap, temporary, poor quality and poor design outcomes. Bland, block like aesthetics come into play, which arises from the perceived standardisation and unitisation of offsite approaches and further instils a preconception that offsite brings a lack of flexibility and design excellence. 2D systems are not excluded and are often thought of as a rudimentary form of construction.
There is good news, and it is reassuring to see that we do not have to look too far to dispel such preconceptions and break down the barriers surrounding offsite approaches.
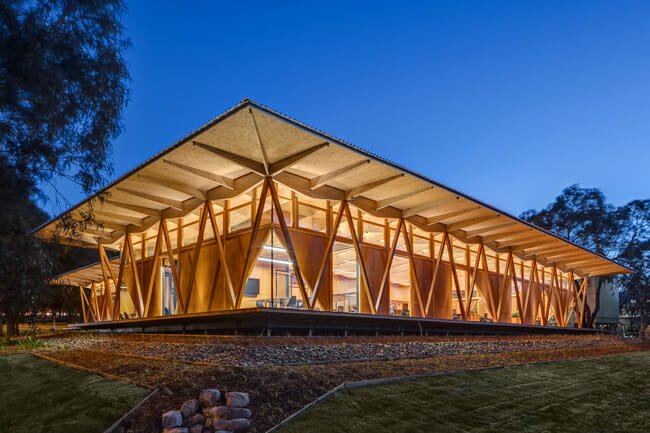
Take the Macquarie University Incubator, designed by Architectus and completed by Lipman in August 2017. The building adopts a 2D hybrid system utilising mass timber roof cassettes, floor cassettes and prefabricated façade panels. A result which strongly opposes the preconceptions identified above.
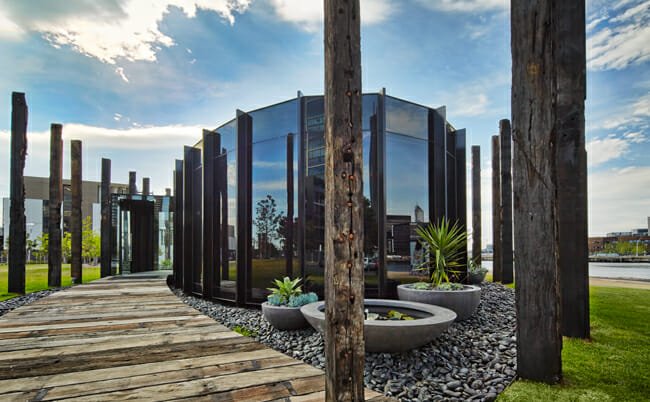
Take the Macquarie University Incubator, designed by Architectus and completed by Lipman in August 2017. The building adopts a 2D hybrid system utilising mass timber roof cassettes, floor cassettes and prefabricated façade panels. A result which strongly opposes the preconceptions identified above.
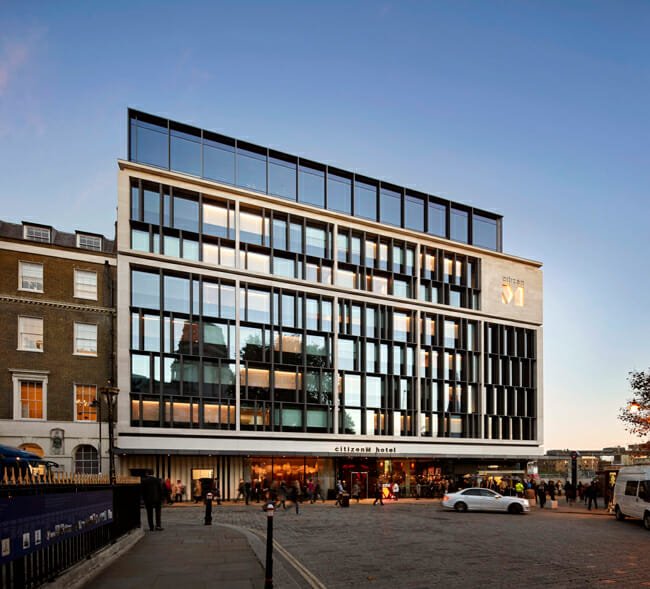
Further abroad, I had the opportunity to stay in the Citizen M Tower of London – a 370 room hotel utilising a volumetric modular approach. To the untrained eye of the end user, the hotel had the look and feel of a traditional approach. Any persistence of social stigma typically associated with offsite approaches quickly disappeared, the precision of an offsite approach being demonstrated through the corridor finish with no indication of joints between modules. Admittedly in this case (and being hyper critical), I did note a marginal change in floor stiffness at midspan of the modules – something that requires careful consideration in the performance specifications.
Imagine the end user recognising an offsite project simply for the superior quality outcomes over a traditional build.
Ultimately, I imagine the end user will recognise and identify an offsite project simply for the superior quality outcomes over a traditional build. In fact, I don’t think we are too far off, over in the United States Jennifer Lund of Marriott Hotels indicated that financiers are requesting to specifically finance offsite projects. A clear demonstration that barriers are breaking down and the value of an offsite approach is being realised.
James is an Associate Director with TSA Management, a project management and advisory services group. James has recently undertaken an extensive review of global offsite manufacturing practices and its impact on project procurement in the Australian built environment. James sees significant opportunity to harness the benefits offsite approaches can bring to a project – predictability and precision of time, cost and quality outcomes which in turn lead to enhanced environmental, sustainability, work health safety, and employee wellbeing outcomes.