Offsite Insights – A Defining Moment
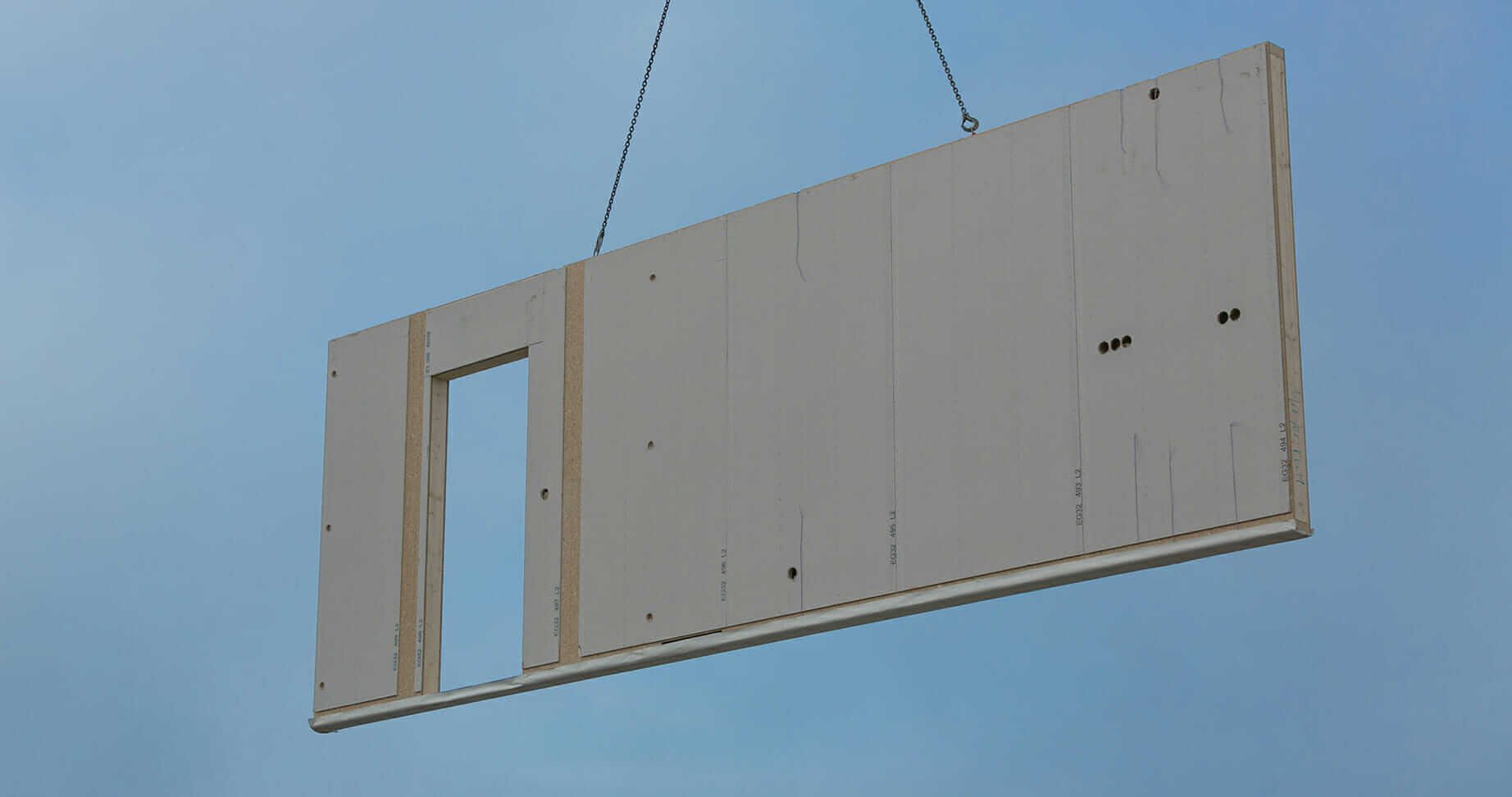
As part of the TSA Management SMART Prize, James Marsden Associate Director investigated the global practices of offsite manufacturing and its impact on project procurement particularly in the context of the Australian built environment. The Offsite Insights series is an extension of this, sharing the learnings through a series of opinion pieces with the intent to kick-start a conversation such that offsite gradually becomes a mainstream conversation.
A defining moment
Getting the terminology right from the outset is key, hence today’s defining moment. It ensures we are all talking the same language, and we are all on the same page.
For the purpose of this forum the term ‘offsite’ will be embraced. You will come across numerous terms within the industry and across the globe when discussing offsite.
prefab, prefabrication, premanufacture, offsite fabrication, offsite construction, modern methods of construction, MMC, offsite, offsite manufacturing, OSM
Personally, I am a fan of offsite manufacturing or OSM. For me, the inclusion of the term ‘manufacturing’ references a much needed shift in mindset pertaining to the construction phase – manufacturing a kit-of-parts for assembly onsite. Given we are not quite there yet in Australia, we will keep it simple with the term ‘offsite’.
In any case, all the above terms are interchangeable and refer to a methodology. This is an important point – offsite is a methodology, it is a method of construction. In short, it refers to any part of the construction process which is taken offsite, manufactured within a controlled environment and later assembled onsite.
Offsite can be applied to any project, it is easy to see why Mark Farmer and similarly the Modular Construction Codes Board (MCCB) take a very liberal view when defining offsite. Mark describing it as “all processes which reduce the level of onsite labour intensity and delivery risk”. Offsite is a methodology which is agnostic to the type of project being delivered.
Types of offsite vary and continually evolve with technological advances and innovative new ways to assemble projects within the built environment. It is best to think about types of offsite methodologies as two or three dimensional (2D or 3D), and structural or non-structural systems. Below is a summary of the types of offsite methods you will come across
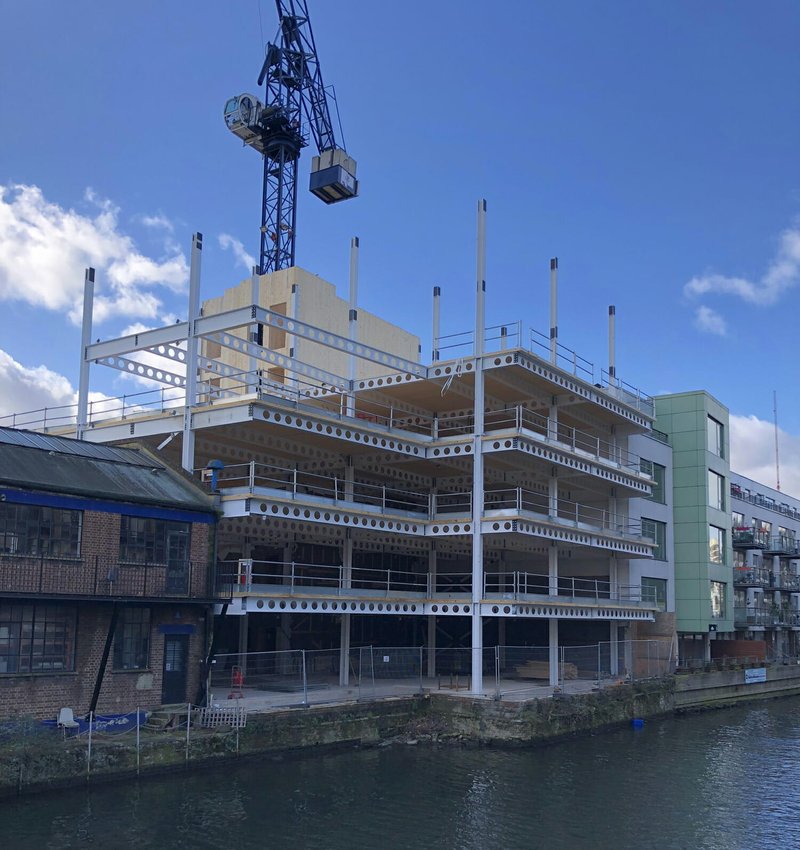
Frame systems – two-dimensional (2D) structural components. Typically stick-based premanufactured elements such as precast concrete, steel, cross laminated timber (CLT), or hybrid combinations thereof.
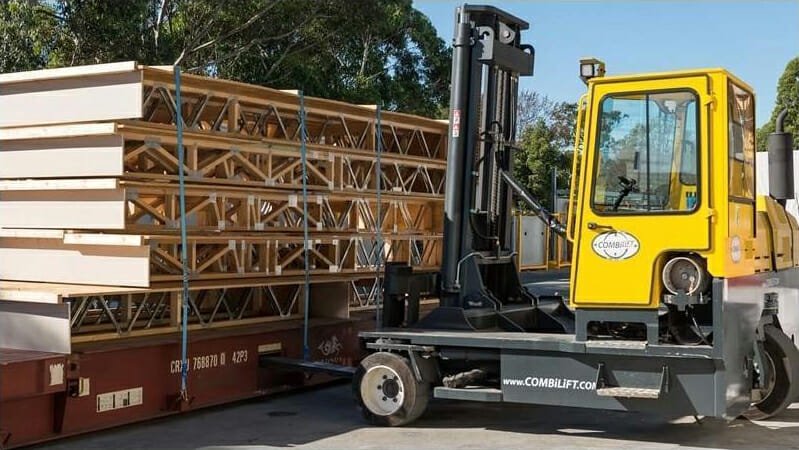
Panel systems – two-dimensional (2D) structural and non-structural panelised elements. Such systems include structural insulated panels (SIPS), floor / wall / roof cassettes, open or closed cassette options, and façade elements. Liken it to the flat-pack approach of Ikea.
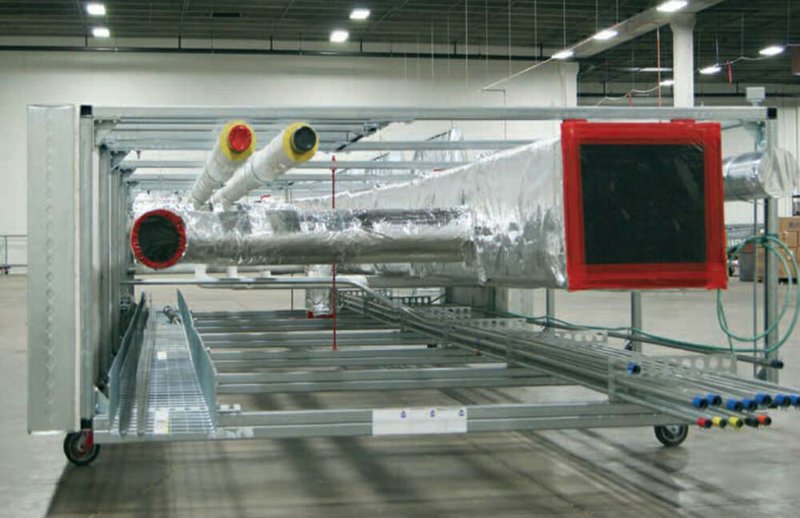
Modular services – two or three-dimensional (2D or 3D) non-structural modular service systems. They offer a “plug and play” solution for use within panel systems, pods and volumetric modules, or standalone risers, distribution racks and plant rooms.
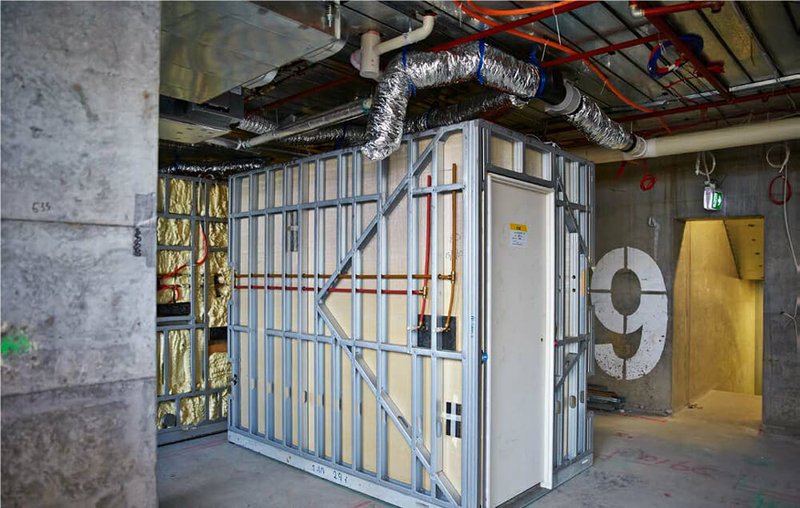
Pods – three-dimensional (3D) non-structural modules. They are complete, fully fitted out modular building elements, typically comprising bathroom, kitchen, laundry or utility pods.
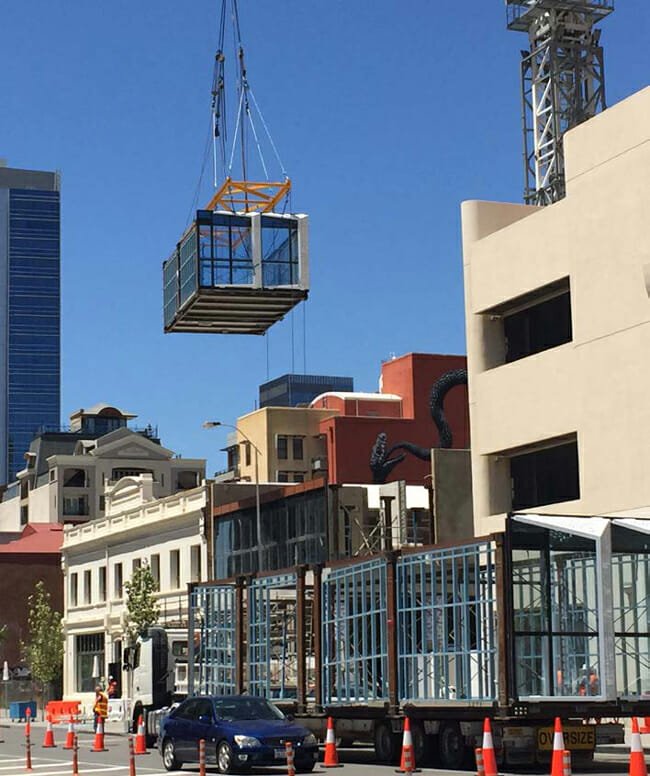
Modular systems – three-dimensional (3D), structural, cold shell building systems typically incorporating structure and façade elements.
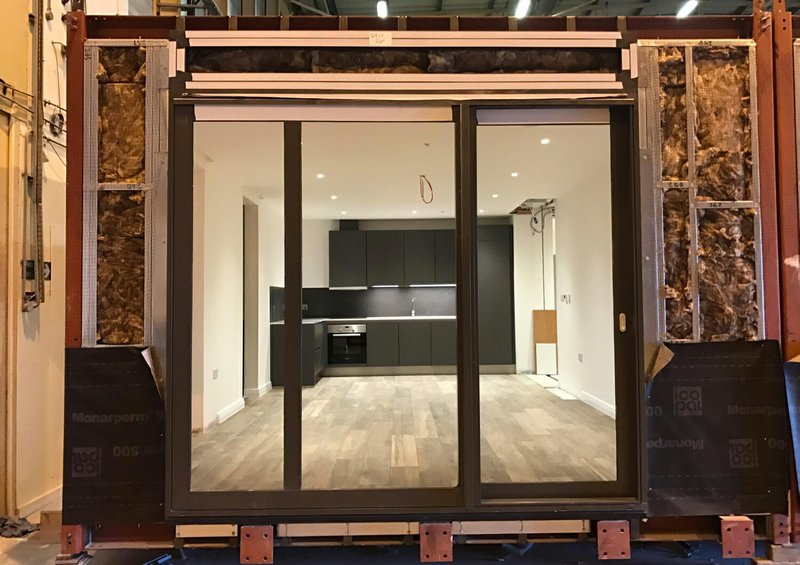
Volumetric modules – three-dimensional (3D) structural modules, commonly referred to as volumetric modular building systems. They comprise warm shell systems, complete and fully fitted out large building elements including combinations of living and working spaces, ensuites, circulation and other functional areas.
For more detailed information regarding offsite terms and definitions, check out Jamie Parr’s “Introduction to Offsite” articles, prefabAUS website, PrefabNZ resources page, and the MCCB handbook.